cGMP Certification
ASI can assist with cGMP audits and certification by offering comprehensive evaluation and compliance services to ensure that manufacturing practices meet regulatory requirements and industry standards, resulting in cGMP certification.
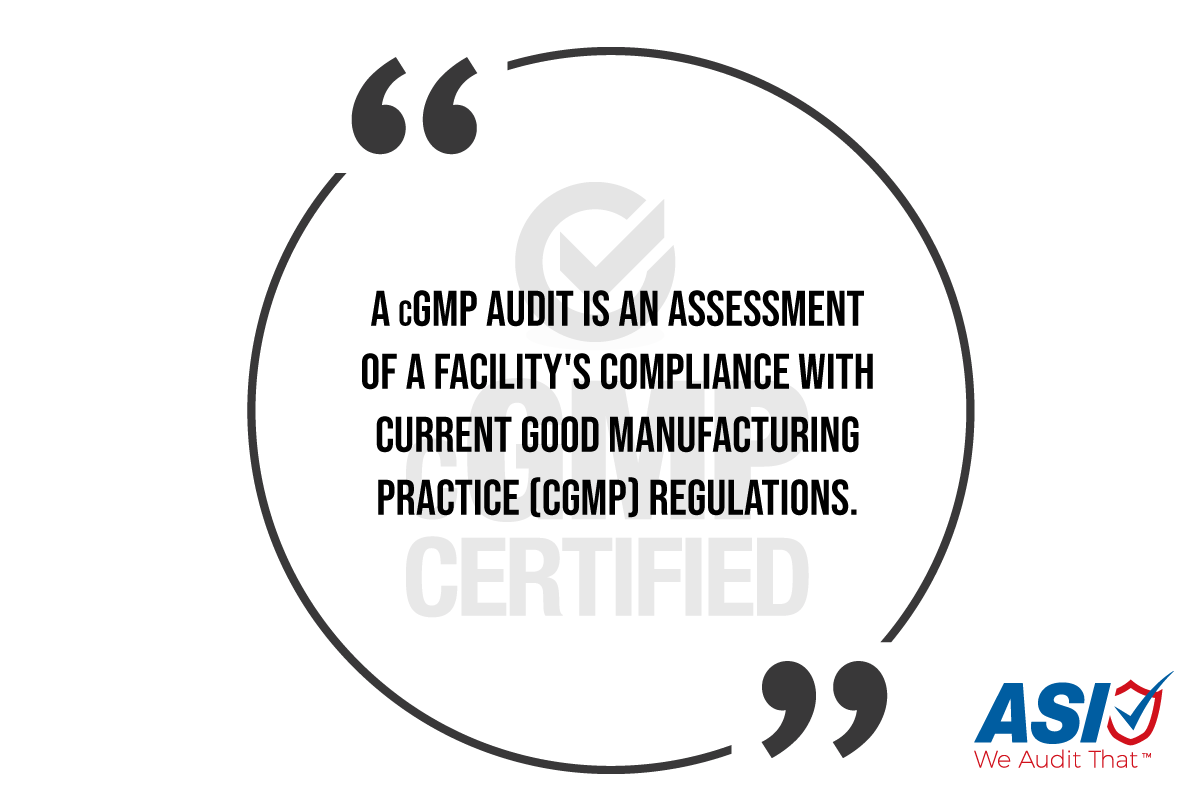
Lets Talk cGMP
At ASI, we use the term cGMP (Current Good Manufacturing Practices) as opposed to the outdated term GMP (Good Manufacturing Practices), because we recognize that safety and quality best practices are constantly changing, and it's our job to constantly be up-to-date on requirements.
cGMP is the first line of defense in keeping your product safe. Regardless of the product type, ALL food manufacturers and service professionals are required to follow cGMP according to the Code of Food Regulations (CFR).
FDA and USDA Auditors will be looking for implementation of these practices. Failure to follow these practices puts your product and business at risk.
cGMP Audit Overview:
A cGMP audit is an assessment of a facility's compliance with current Good Manufacturing Practice (cGMP) regulations.
During a cGMP audit, a qualified auditor will review the facility's operations, processes, and documentation to ensure that they meet cGMP requirements. The auditor will evaluate various aspects of the facility, including:
- Equipment and facility maintenance: The auditor will evaluate the facility's equipment and infrastructure to ensure that they are properly maintained and cleaned.
- Documentation: The auditor will review documentation related to production, quality control, and testing to ensure that it is complete, accurate, and properly maintained.
- Standard operating procedures: The auditor will review the facility's standard operating procedures (SOPs) to ensure that they are up-to-date and accurately reflect the facility's processes.
- Personnel: The auditor will review the facility's personnel training records and qualifications to ensure that they are adequate for the tasks being performed.
- Quality control: The auditor will review the facility's quality control procedures to ensure that they are adequate for maintaining product quality and safety.
cGMP CERTIFICATION:
At ASI, we use the term cGMP (Current Good Manufacturing Practices) as opposed to the outdated term GMP (Good Manufacturing Practices), because we recognize that safety and quality best practices are constantly changing, and it's our job to constantly be up-to-date on requirements. cGMP is the first line of defense in keeping your product safe.
Regardless of the product type, ALL food manufacturers and service professionals are required to follow cGMP according to the Code of Food Regulations (CFR). FDA and USDA Auditors will be looking for implementation of these practices. Failure to follow these practices puts your product and business at risk.
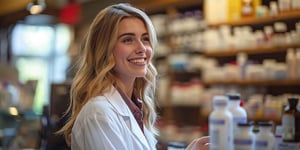
Contact ASI for a customized cGMP services quote.
Requesting a cGMP services quote from ASI helps ensure compliance with strict manufacturing standards, safeguarding product quality and boosting operational excellence.
WHAT IS A cGMP AUDIT?
A cGMP audit is an assessment of a facility's compliance with current Good Manufacturing Practice (cGMP) regulations.
During a cGMP audit, a qualified auditor will review the facility's operations, processes, and documentation to ensure that they meet cGMP requirements. The auditor will evaluate various aspects of the facility, including:
- Equipment and facility maintenance: The auditor will evaluate the facility's equipment and infrastructure to ensure that they are properly maintained and cleaned.
- Documentation: The auditor will review documentation related to production, quality control, and testing to ensure that it is complete, accurate, and properly maintained.
- Standard operating procedures: The auditor will review the facility's standard operating procedures (SOPs) to ensure that they are up-to-date and accurately reflect the facility's processes.
- Personnel: The auditor will review the facility's personnel training records and qualifications to ensure that they are adequate for the tasks being performed.
- Quality control: The auditor will review the facility's quality control procedures to ensure that they are adequate for maintaining product quality and safety.
cGMP OVERVIEW:
ASPECT | DESCRPTION |
What is cGMP Certification? | A formal recognition that a manufacturer complies with the regulations and quality standards set by regulatory agencies like the FDA. |
Purpose of cCMP | Ensures products are consistently produced and controlled according to strict quality standards, minimizing contamination, errors, and defects. |
Industries and cGMP Certification |
|
Key Areas Covered by cGMP |
|
Benefits of cGMP Certification | Demonstrates commitment to high-quality production standards and compliance with regulatory expectations, building trust with consumers and regulatory bodies. |
ASI Audit | ASI conducts thorough audits to assess cGMP compliance, identifying gaps and providing actionable insights for improvement. |
How ASI Helps | ASI's audits ensure companies understand cGMP requirements, enhance operational efficiency, and achieve compliance, ultimately fostering product safety and quality. |
HOW TO PREPARE FOR cGMP AUDIT.
Preparing for a cGMP (current Good Manufacturing Practices) audit is crucial to ensure compliance with regulatory standards and maintain the quality of products. Here are steps to help you prepare effectively for a cGMP audit:
1 - Understand cGMP Requirements:
Thoroughly familiarize yourself with cGMP regulations relevant to your industry. Review guidelines provided by regulatory bodies such as the FDA or EMA to understand the specific requirements.2 - Conduct Internal Audits:
Perform regular internal audits to identify gaps or non-compliance issues within your manufacturing processes. Address any deficiencies found during these audits before the official cGMP audit.3 - Document Management:
Ensure all required documentation, including Standard Operating Procedures (SOPs), batch records, and quality control records, is organized, accurate, and readily accessible for inspection.4 - Employee Training and Awareness:
Train employees on cGMP guidelines and ensure they understand their roles in maintaining compliance. Regular training sessions and awareness programs help in fostering a compliance-oriented culture.5 - Facility Readiness:
Inspect your manufacturing facility to ensure it meets cGMP standards for cleanliness, sanitation, equipment maintenance, and environmental controls. Address any deficiencies promptly.6 - Supplier Audits and Quality Control:
Evaluate and ensure that your suppliers and vendors also adhere to cGMP standards. Implement robust quality control measures for incoming materials and components.7 - Risk Assessment and Corrective Actions:
Conduct risk assessments to identify potential vulnerabilities in your processes. Implement corrective and preventive actions (CAPAs) to address any identified risks.8 - Mock Audits or Pre-Audit Preparation:
Conduct mock cGMP audits internally or hire a third-party auditor to simulate the official audit. This exercise helps identify areas for improvement and ensures readiness.9 - Continuous Improvement:
Establish a system for continuous improvement. Regularly review and update procedures based on audit findings, industry updates, and best practices.10 - Engage Expert Consultants:
Consider engaging consultants or experts specializing in cGMP compliance to assist in preparation and ensure adherence to the latest regulatory requirements.11 - Schedule ASI cGMP Audit
By diligently following these steps, your organization can significantly enhance its readiness for a cGMP audit, ensuring compliance with regulations and maintaining the highest quality standards in cGMP.
HOW TO PREPARE FOR cGMP AUDIT:
- Understand relevant cGMP regulations for your industry.
- Appoint a dedicated audit preparation team.
- Conduct internal audits to identify non-compliance issues.
- Maintain organized and accurate documentation.
- Ensure employees are well-trained in cGMP requirements.
- Regularly maintain facilities and equipment.
- Evaluate supplier cGMP compliance.
- Update and review quality control and testing protocols.
- Conduct mock audits to identify and address issues.
- Implement corrective and preventive actions (CAPA) for deficiencies.
- Prepare necessary audit documents and policies.
- Schedule the audit and understand its scope.
- Be transparent and cooperative on the audit day.
- Address audit findings promptly with a corrective action plan.
The following are the cGMP audit services ASI provides:
cGMP Food Safety Mock Audit – The auditor will walk through the cGMP food safety audit process, go over every question on the audit form and help you prepare for a scored audit. This is for clients that have not had audits before, are new to the industry or have not had an audit in a while.
cGMP Food Safety Scored Audits – ASI can perform the scored audit to satisfy your customer’s requirements. We offer different types of cGMP food safety audits specific to the facility being audited. Most companies require audits annually.
Customized Food Safety Audit Forms – Our experts can customize audit forms and audit programs for your different facilities and supply chains. The criteria can include your company policies and procedures so all locations comply with the cGMPs and management guidelines. Companies perform these audits annually, semi-annually and quarterly.
Supplier Programs – we can ensure that your products are being safely handled and protected following the cGMPs throughout your supply chain. Companies perform these food safety audits annually, semi-annually and quarterly.
What are the ADVANTAGES of cGMP Certification?
Besides meeting regulatory and customer requirements, there are numerous other benefits to receiving a cGMP audit. Some of these benefits include the following:
- Improved quality control: cGMP certification requires strict adherence to quality control processes, which can help improve product quality and reduce the risk of defects and product recalls.
- Increased customer trust: cGMP certification is recognized globally and can help build customer trust by demonstrating that a company is committed to producing high-quality products that meet regulatory requirements.
- Better product consistency: cGMP certification requires standardized processes for product manufacturing and testing, which can help ensure consistent product quality and reduce variability in product performance.
- Competitive advantage: cGMP certification can help companies stand out from competitors and win contracts with customers who require or prefer cGMP-certified suppliers.
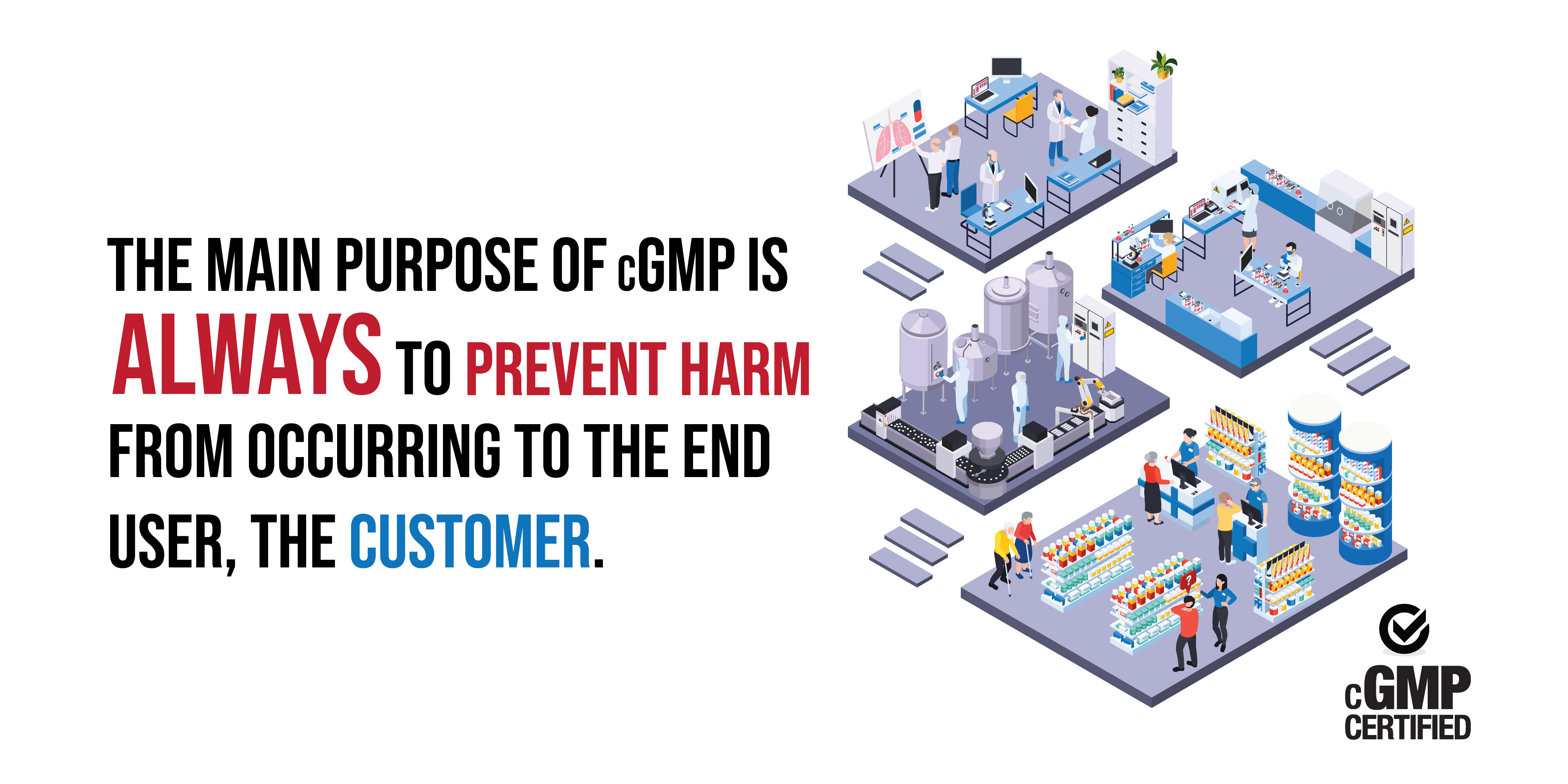
Lets Talk cGMP
At ASI, we use the term cGMP (Current Good Manufacturing Practices) as opposed to the outdated term GMP (Good Manufacturing Practices), because we recognize that safety and quality best practices are constantly changing, and it's our job to constantly be up-to-date on requirements.
cGMP is the first line of defense in keeping your product safe. Regardless of the product type, ALL food manufacturers and service professionals are required to follow cGMP according to the Code of Food Regulations (CFR).
FDA and USDA Auditors will be looking for implementation of these practices. Failure to follow these practices puts your product and business at risk.
cGMP Audits ASI Offers:
- Distribution and Warehouse
- Food Processing
- Food Packaging
- Dietary Supplements
- Pet food/Animal Feed
- Cannabis
- Supplier Specific Audits
WHAT ARE THE ADVANTAGES OF cGMP CERTIFICATION?
Besides meeting regulatory and customer requirements, there are numerous other benefits to receiving a cGMP audit. Some of these benefits include the following:
- Improved quality control: cGMP certification requires strict adherence to quality control processes, which can help improve product quality and reduce the risk of defects and product recalls.
- Increased customer trust: cGMP certification is recognized globally and can help build customer trust by demonstrating that a company is committed to producing high-quality products that meet regulatory requirements.
- Better product consistency: cGMP certification requires standardized processes for product manufacturing and testing, which can help ensure consistent product quality and reduce variability in product performance.
- Competitive advantage: cGMP certification can help companies stand out from competitors and win contracts with customers who require or prefer cGMP-certified suppliers.
- COST
- TIME
AVERAGE cGMP AUDIT COST
The cost of a Current Good Manufacturing Practices (cGMP) audit can vary significantly based on several factors such as the scope of the audit, the size and complexity of the facility, the location, the expertise of the auditing firm or individual conducting the audit, and any additional services required.
On average, a basic cGMP audit might start from a few thousand dollars and can range up significantly depending on the depth of the audit, the duration, travel expenses (if applicable), the reputation of the auditing firm, and any specialized expertise required.
It's essential to discuss the specific needs of your facility and the scope of the audit with auditing firms or professionals to get accurate cost estimates tailored to your situation. This ensures you receive an appropriate and comprehensive service within your budget.
AVERAGE cGMP AUDIT TIMEFRAME
The duration of a Current Good Manufacturing Practices (cGMP) audit, similar to a GMP audit, can vary depending on several factors:
-
Size and Complexity of the Facility: Larger facilities or those with complex operations might require a longer audit duration compared to smaller, less complex ones.
-
Scope of the Audit: The depth and breadth of the audit, covering various departments, processes, and documentation, will impact its duration. A comprehensive audit will take longer than a more focused one.
-
Preparation Time: The auditing team might require additional time for pre-audit preparations, such as reviewing documentation and scheduling.
-
Audit Findings and Discussions: If significant issues or findings are identified during the audit, additional time might be necessary for discussions, clarification, and resolution.
Typically, a cGMP audit can range from a few days to multiple weeks. Shorter audits might take around 1-5 days for smaller or more focused assessments, while larger or more complex facilities might require a week or more for a comprehensive evaluation.
The specific duration for a cGMP audit would be determined during the planning phase, considering the factors mentioned above and tailoring the audit scope to meet the specific needs of the facility being audited.